Why plastic extrusion is ideal for mass production
Why plastic extrusion is ideal for mass production
Blog Article
Key Advantages and Considerations of Executing Plastic Extrusion in Your Jobs
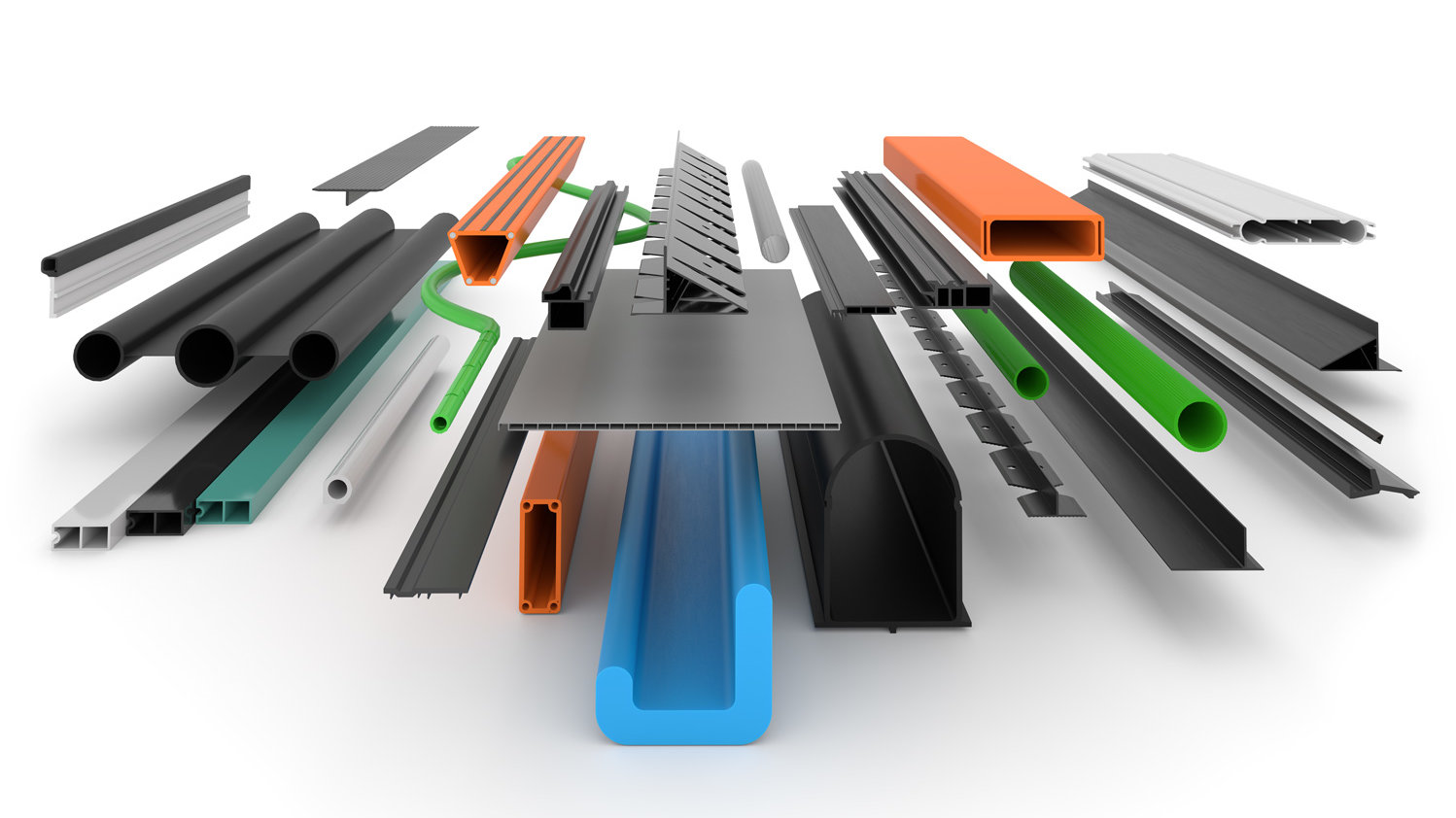
Recognizing the Essentials of Plastic Extrusion
Plastic extrusion, a staple in the production market, is a process that includes melting raw plastic material and reshaping it right into a continuous account. This profile, as soon as cooled down, can be reduced into wanted sizes or curled for later usage. The appeal of plastic extrusion depends on its versatility. A large range of items, from piping to window structures, can be produced. The procedure needs an extruder, a complex maker with a heated barrel, a turning screw, and a die at the end. The plastic material, in the form of pellets, is fed right into the extruder, where it's melted and compelled via the die, taking its shape. The choice of plastic and the design of the die figure out the item's qualities.

The Economic Benefit of Plastic Extrusion
The economic benefit of plastic extrusion exists mostly in 2 locations: economical product manufacturing and helpful production rates. With plastic extrusion, companies can create high volumes of product at a lower cost contrasted to other approaches. The procedure flaunts an excellent production speed, dramatically minimizing time and further boosting its financial feasibility.
Cost-Effective Product Production
A significant benefit of plastic extrusion is its amazing cost-effectiveness. This manufacturing procedure permits for constant, high-volume production with minimal waste, which converts into reduced prices. The raw materials made use of, usually plastic pellets, are reasonably cost-effective contrasted to various other substances (plastic extrusion). The procedure itself needs much less power than several other manufacturing methods, better reducing costs. Additionally, the extrusion procedure allows for a high level of precision in forming the plastic, decreasing the requirement for pricey post-production alterations or modifications. The sturdiness and long life of extruded plastic items commonly indicate less need for replacements, adding to long-term financial savings. All these factors make plastic extrusion a highly affordable choice for numerous projects, offering an appealing equilibrium between expense and performance.
Beneficial Manufacturing Speeds
While preserving the cost-effectiveness of the materials, another noteworthy benefit of plastic extrusion exists in its fast manufacturing rates. This combination of quality, cost-effectiveness, and speed highlights the significant economic benefit of carrying out plastic extrusion in numerous jobs.
Convenience and Personalization: The Staminas of Plastic Extrusion
One of the prominent toughness of plastic extrusion lies in its adaptability and customization potential. These qualities unlock to endless style possibilities, offering suppliers the ability to tailor products to certain demands. This heightened level of personalization not just improves product performance but also dramatically increases product uniqueness.
Endless Layout Opportunities
Plastic extrusion shines in its ability to provide almost limitless design possibilities. Plastic extrusion can deal with a variety of plastic types, expanding its application extent. With plastic extrusion, the design possibilities are practically countless.
Increasing Item Individuality
The versatility of plastic extrusion can greatly enhance product individuality. This procedure enables developers to explore various shapes, sizes, and shades, offering them the liberty to develop special products that stick out on the market. It is this personalization that provides an unique identification per item, differentiating it from its competitors.
In addition to its visual advantages, the customizability of plastic extrusion additionally provides practical advantages. Designers can modify the buildings of the plastic according to the details requirements of their website the application, enhancing the product's functionality. They can make the plastic much more adaptable, much more durable, or a lot more immune to warmth, depending on what the product calls for. Therefore, plastic extrusion not just improves product individuality however also its energy and marketability.
Style Limitations in Plastic Extrusion: What You Need to Know
Just how can design constraints potentially impact the process of plastic extrusion? While plastic extrusion is flexible, layout restrictions can cut its benefits. Certain complex styles might not be feasible due to the restrictions of the extrusion process, potentially limiting the creation of complex profiles. The process is much less ideal for hollow or multi-chambered structures. In addition, the extrusion process may not always give the preferred surface area coating, particularly for those needing high gloss or optical quality. Product selection can likewise present obstacles, as not all polymers are suitable for extrusion. High-temperature immune plastics, for instance, might present difficulties. Recognizing these restrictions is essential for effective application of plastic extrusion in your jobs. plastic extrusion.
Examining the Ecological Influence of Plastic Extrusion
While recognizing layout limitations is a substantial facet of plastic extrusion, it is just as crucial to consider its ecological effects. The procedure of plastic extrusion entails melting plastic products, possibly releasing harmful gases right into the atmosphere. Additionally, the resulting products are frequently non-biodegradable, adding to landfill waste. However, advancements in modern technology have actually enabled for more environmentally-friendly practices. As an example, utilizing recycled plastic materials in the extrusion procedure can decrease ecological impact. Additionally, establishing naturally degradable plastic options can aid alleviate waste issues. Evaluating these ecological aspects is vital when executing plastic extrusion tasks, making sure a balance in between effectiveness, cost-effectiveness, and ecological obligation.
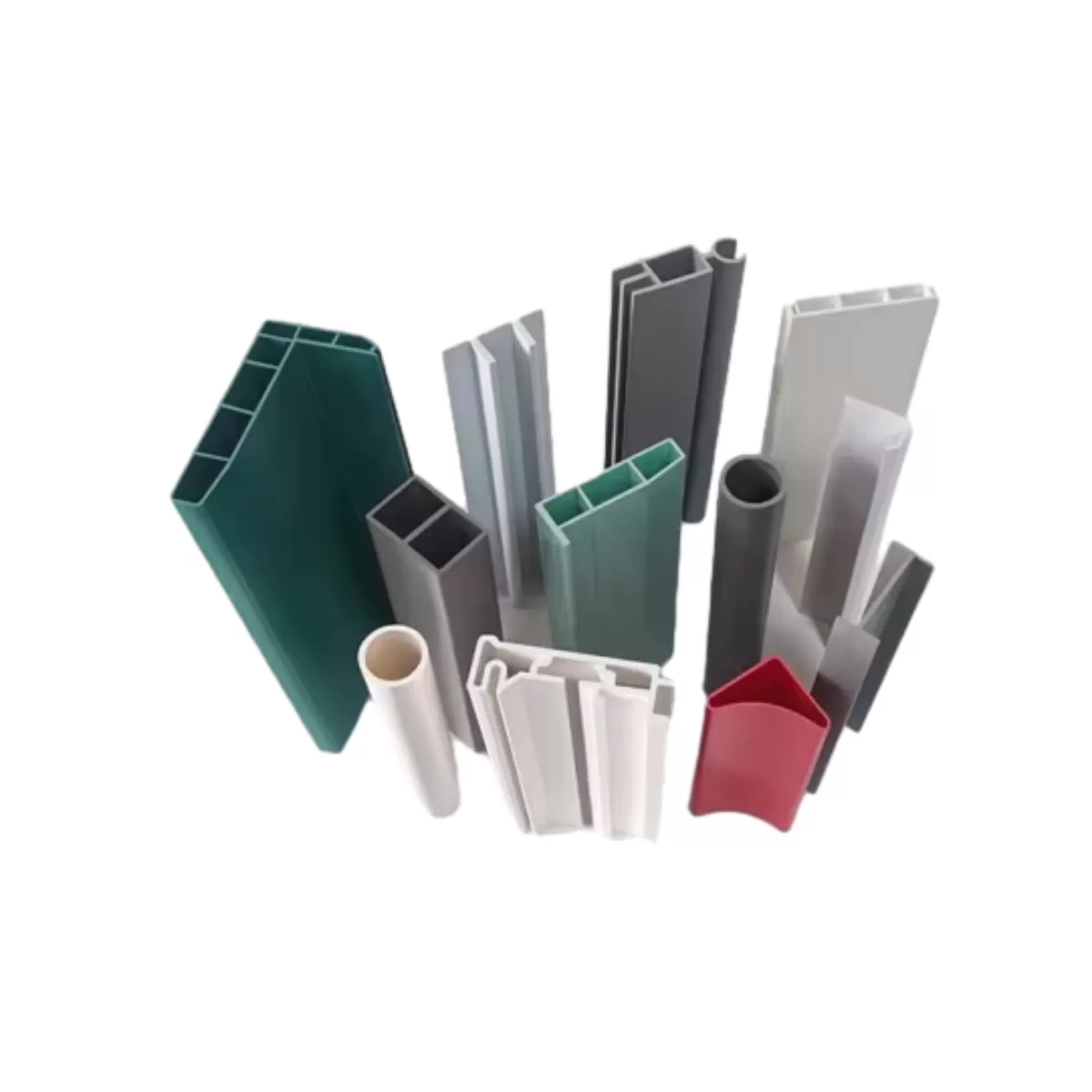
Study: Successful Projects Using Plastic Extrusion
Success tales in the area of plastic extrusion abound, showing both the convenience and efficiency of this manufacturing process. plastic extrusion. Another effective situation is the production of plastic movie for packaging and agriculture. These instances highlight plastic extrusion's important role in numerous fields, proving to its versatility, cost-effectiveness, and reputable output.
Verdict
In conclusion, plastic extrusion uses a reliable and economical method for creating intricate forms with very little waste. Including plastic extrusion into jobs can lead to effective end results, as shown by various case studies.
Plastic extrusion, a staple in the production sector, is a procedure that involves melting raw plastic material and reshaping it into a constant account. Plastic extrusion can deal with a range of plastic kinds, increasing its application scope.Exactly how useful content can develop constraints possibly influence the procedure of plastic extrusion? The procedure of plastic extrusion involves melting that site plastic products, possibly releasing unsafe gases into the environment. Using recycled plastic products in the extrusion procedure can decrease environmental effect.
Report this page